
This document details the progress to date on the program entitled ''SMALLER FOOTPRINT DRILLING SYSTEM FOR DEEP AND HARD ROCK ENVIRONMENTS FEASIBILITY OF ULTRA-HIGH SPEED DIAMOND DRILLING'' for the period starting Jthrough September 30, 2004. The highest rotary speed systems in oil field and mining drilling and coring today run less than 10,000 rpm-usually well below 5,000 rpm. The drilling and coring industry today does not practice this technology. The significance of the ''ultra-high rotary speed drilling system'' is the ability to drill into rock at very low weights on bit and possibly lower energy levels. The net result for operators is improved profit margin as well as an improved position on reserves. Thus potential savings of $200 MM to $600 MM are possible if drilling rates are doubled. An estimate of North American hard rock drilling costs is in excess of $1,200 MM. For domestic operations involving hard rock and deep oil and gas plays, improvements in penetration rates is an opportunity to reduce well costs and make viable certain field developments.
#Gun drill parameters full#
Adaptation to the oilfield will require innovative bit designs for full hole drilling or continuous coring and the eventual development of downhole ultra-high speed drives.
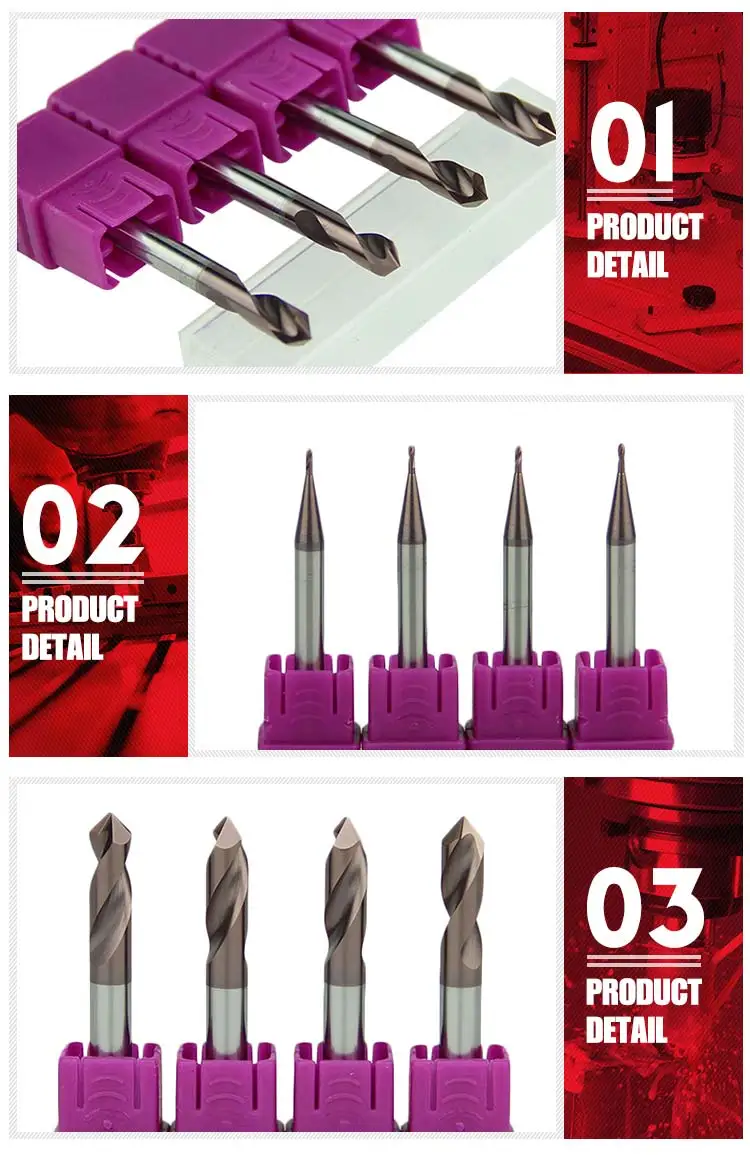
TerraTek successfully tested ultrahigh speed (40,000 rpm) small kerf diamond coring.
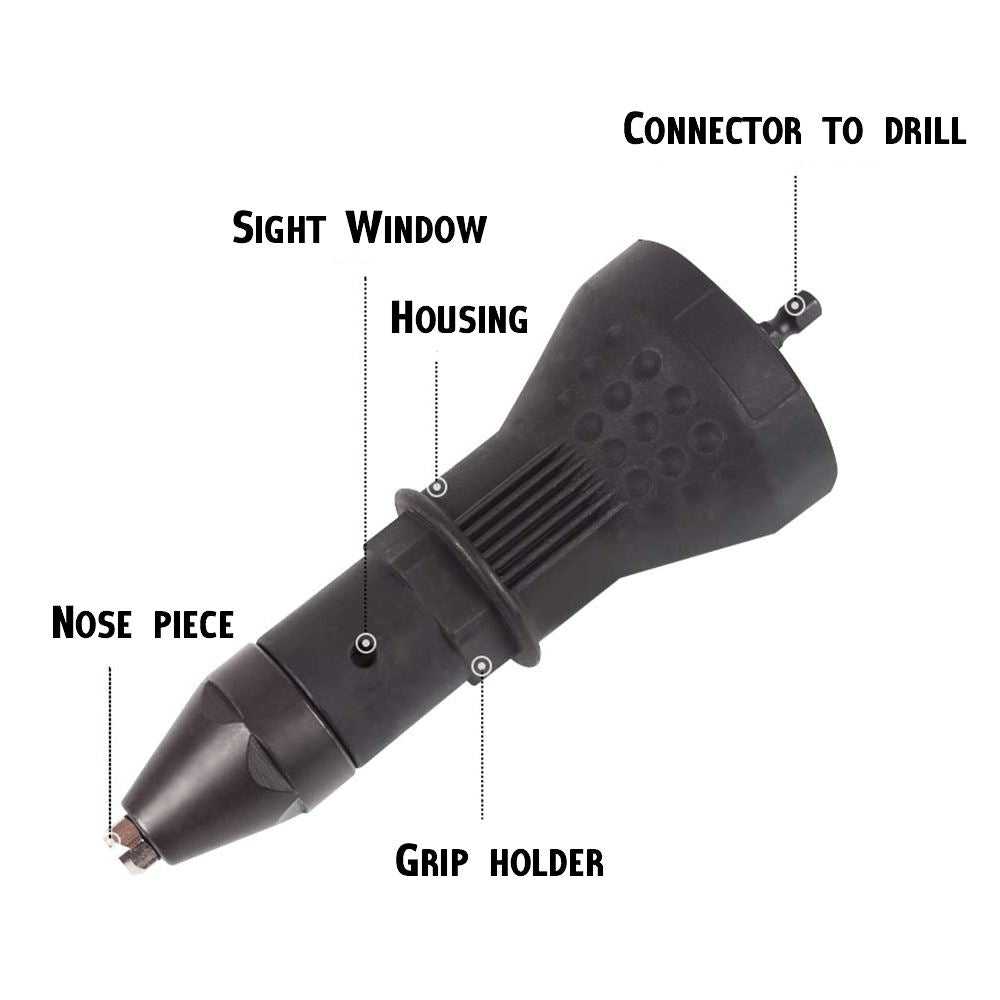
The objective of that program was to demonstrate miniaturization of a robust and mobile drilling system that expends small amounts of energy. The project draws on TerraTek results submitted to NASA's ''Drilling on Mars'' program. The principle focus is on demonstration testing of diamond bits rotating at speeds in excess of 10,000 rpm to achieve high rate of penetration rock more » cutting with substantially lower inputs of energy and loads. The work includes a feasibility of concept research effort aimed at development and test results that will ultimately result in the ability to reliably drill ''faster and deeper'' possibly with rigs having a smaller footprint to be more mobile. TerraTek believes that significant improvements in drilling deep hard rock will be obtained by applying ultra-high (greater than 10,000 rpm) rotational speeds.

The two phase program addresses long-term developments in deep well and hard rock drilling. The cutting inserts of each gage row include relatively large cutting faces in the direction of the sidewalls of the bore hole in order to have substantial surface contact with the gage of the bore hole. This extended gage row construction enables the gage inserts to cut into any sloping wall to produce a sharp corner and bring the hole back into line with the drill string. The gage row of each cone extends further out from the cone axis than any more » of the intermediate adjacent rows in such a manner that the annular area of the hole bottom cut by the gage inserts is lower than any other area cut by the intermediate rows of cutting inserts.

The heel portion is of sufficient mass to support the gage row of cutting elements. Each cone cutter further includes a heel portion adjacent the base of the conical surface. A plurality of annular rows of cutting inserts are circumferentially mounted on the conical surface of each cutter. The drill bit includes a plurality of legs with each leg having a cone cutter rotatively supported thereon. A drill bit is disclosed for maintaining a desired direction of drilling or to reduce the deviation already established.
